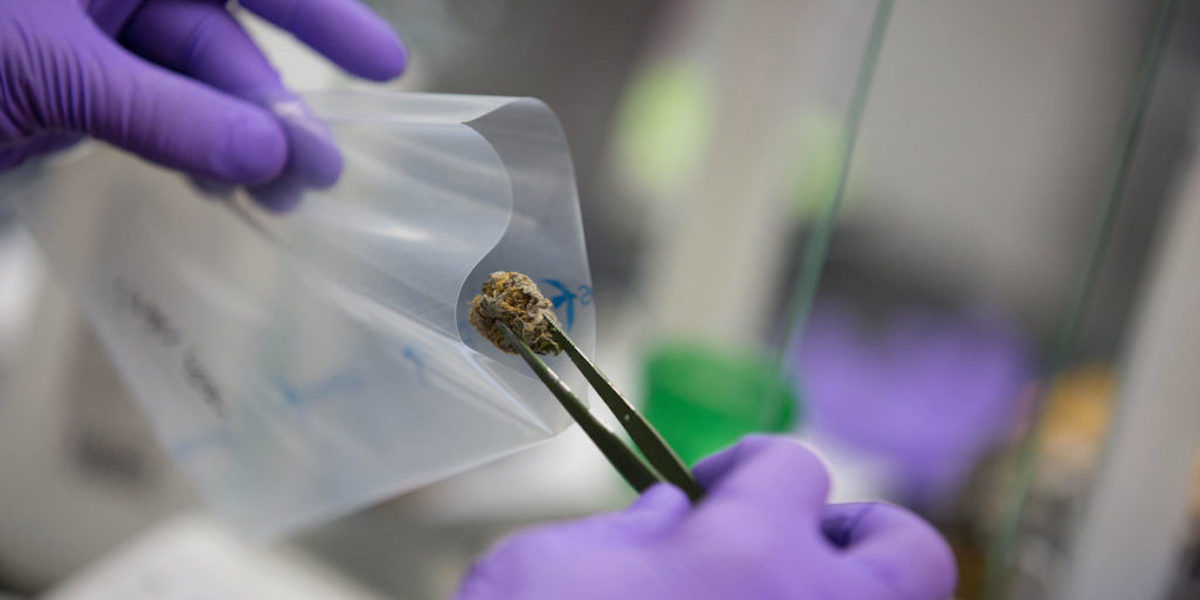
3 min read
An Easy Guide to the Cannabis Testing Requirements in California
All marijuana in California must pass specific cannabis testing requirements before it can be sold in dispensaries as of July 1st, 2018. The end of the transitional exemption period brought with it new rules regarding the amount of pesticides, potency, impurities, and moisture that could be contained in cannabis products.
Distributors are primarily responsible for requesting regulatory testing and have the ability to transport marijuana between licensed cultivators and testing facilities. In an effort to raise awareness of the new cannabis testing requirements, we’ve compiled this easy guide for cannabis industry professionals.
What Tests are Required?
The California Bureau of Cannabis Control has issued their own cannabis testing requirements that breakdown products into: inhalable cannabis, inhalable cannabis product, and other cannabis product.
Flower |
Concentrates |
Edibles, Oils, Tinctures |
Flower Potency |
Concentrate Potency |
Product Potency |
Residual Pesticides |
Residual Pesticides |
Residual Pesticides |
Microbial Impurities |
Microbial Impurities |
Microbial Impurities |
Foreign Ingredients |
Residual Solvents |
Residual Solvents |
Moisture Content |
Foreign Ingredients |
Foreign Ingredients |
Homogeneity *multi-serving products |
How Do I Make Sure the Cannabis is Compliant?
The best way to ensure that your cannabis products are compliant is to use a cannabis testing company to come and collect the samples from the distributors. Most testing facilities provide trained field samplers who have experience in the collection process and will do so with minimal interruption to the day to day operations. Allowing the testing company to send their collectors there is less chance of contamination which could prevent your sample from passing.
What is the Maximum Batch Size?
The maximum batch size depends on the type of product you are testing. If your marijuana product is flower then it will always be measured in pounds. The maximum weight for a batch tops out at 50 lbs, however for sampling purposes these will broken down into increments of 10 lbs each. Cannabis testing requirements mandate that a minimum of .35% of every batch should be collected for sample testing.
The California Department of Food and Agriculture’s Cannabis Cultivation Branch defines a batch as the same strain, composition, or growing conditions.
Harvest Batch Size (lbs.) |
Number of Increments |
10 lbs. or less |
8 |
10.1 – 20.0 |
16 |
20.1 – 30.0 |
23 |
30.1 – 40.0 |
29 |
40.1 – 50.0 |
34 |
All manufactured cannabis goods such as vape cartridges, edibles, tinctures or capsules will be measured by the unit.
Product Batch Size |
Minimum # of Increments |
50 units or less |
2 |
51 – 150 units |
3 |
151 – 500 units |
5 |
501 – 1200 units |
8 |
1,201 – 3,200 units |
13 |
3,201 – 10,000 units |
20 |
10,001 – 35,000 units |
32 |
35,001 – 150,000 units |
50 |
Will my Batch Pass Cannabis Testing?
If you want to make sure that your batch passes all of the cannabis testing requirements, you’ll want to do some research and development testing prior to submitting a sample. R&D is a great way to see if there are any issues with your product before it reaches an official testing facility where all the results must be reported to regulators for approval.
Understanding the cannabis testing requirements will help every link in the supply chain to maintain compliance and keep the consumers protects. All testing results can be entered into the products profile on your dispensary POS software so that customers know they are purchasing products of the highest quality.